- Joined
- Jul 24, 2002
- Messages
- 7,126
Hey Marty:Just not sure how well the carbon would glue as a bottom skin without the plywood. Still thinking about that....
Thanks Terry.... !!!
Good to here you messin' with the CF, you're gonna love it!
If you make small interior/exterior fillets the sheeting will never let go, here's a bulkhead:
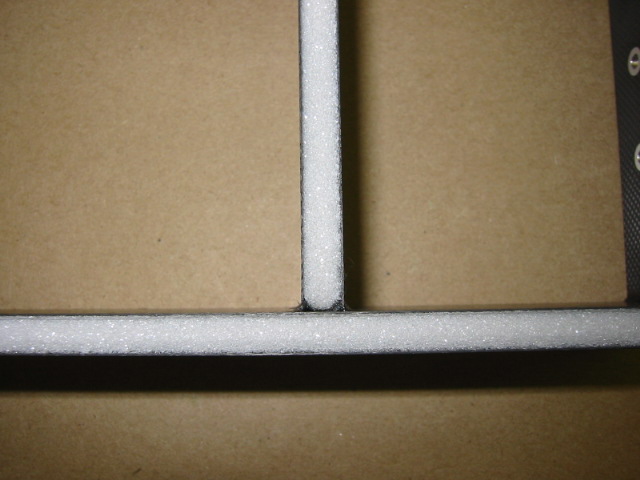
Made a little tool but you could do it freehand:
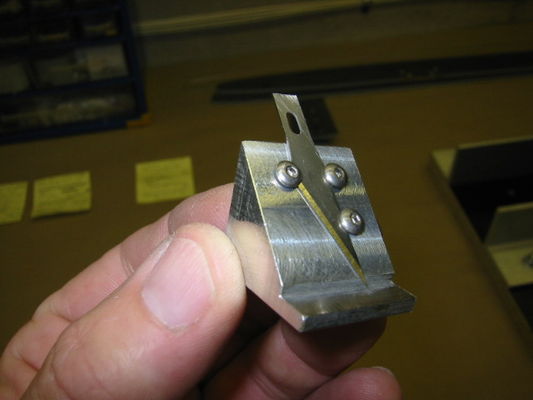
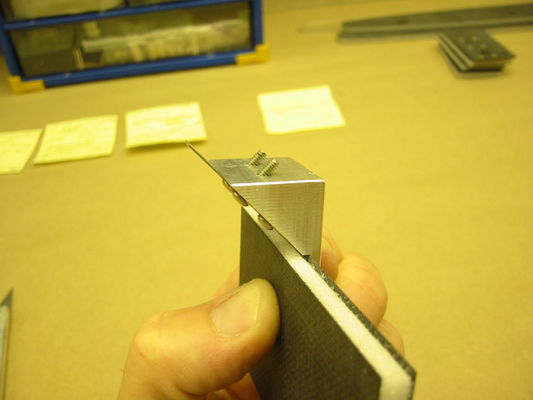
Last edited by a moderator: